Should I track to tray or instrument level?
When people ask me about instrument tracking, there are are number of things I need to find out from them so that I get an idea of what they want to track. So I begin by asking them what they would like to track:
- track preparation and Tray Setup?
- track washing?
- track ultrasonic cleaners?
- sterile items to patients?
I also ask them whether they want to implement 2D Data matrix scanning and whether they want to communicate with Sterilizers and Washers?
Often, people answer YES to all questions.
Finally I ask them what they want from a tracking system, or, to what level do they want to track.
There are generally 2 typical replies to this question.
- I just want to be able to track through washers and sterilizers to the patient
- I want to be able to track at instrument level to patients using 2D data matrix scanning
The thing to consider with the options above is that each has a different cost. Each option has different hardware requirements. The first option will use less sophisticated hardware than the second and is quicker and less costly to implement and will use less resources.
The diagram below shows the 2 main options, Tray Level tracking in blue and Instrument Level tracking in green.
The yellow arrow demonstrates the level of effort required to track through each process.
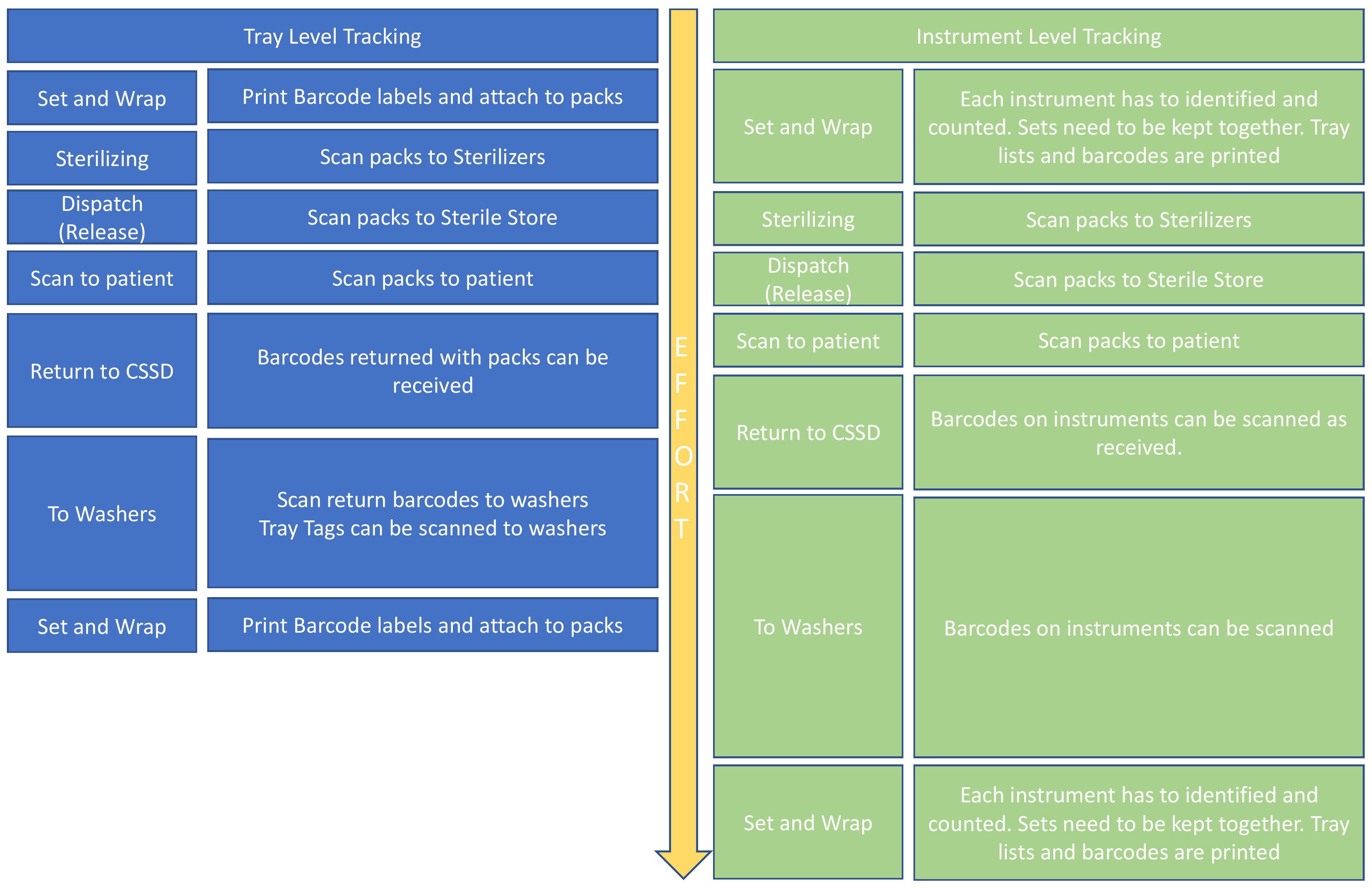
Tray Level Tracking
Looking at the blue tray level tracking section, note that the rectangles are the same height until we hit Return to CSSD and scan to Washers. There are several reasons for this:
- In my experience, it’s quite likely that your current level of tracking in Decon is minimal if at all. Therefore, just going from tracking nothing, to tracking something will require more effort.
- Decon is the most difficult place to track instruments. It's dirty and wet and there are aerosols flying about. It’s a hazardous environment that’s hardly conducive to typing on keyboards and handling scanners.
- There are 2 tracking components here, Tracking Return to CSSD and Tracking to Washers.
Simply just implementing tracking in Decon will require more than your current amount of effort to process items. So, unless you strategise around this reality, tracking in Decon will slow you down and effect turnaround times.
Some of the strategies that you can put in place to minimise the impact on effort are:
- Implementing scannable tray tags
- Returning used Steripeel barcodes with the items coming back from theatre
- Add another FTE
It’s a good idea to be aware of this and budget for an additional FTE in Decon if possible.
The thing that most people don’t consider is that if you go from little or no tracking to a high level of tracking, it’s going to require more resources.
The tradeoff of course is that you will have world best practice tracking.
Instrument Level Tracking
Looking at the green instrument level tracking section, you can see that the "Set and Wrap" section is larger than that of the set and wrap section in blue.
There are several reasons for this:
- Every instrument has a 2D data matrix barcode on it.
- Each instrument must be individually identified and counted
- Sets now need to be kept together
- Trays lists need to be checked off and printed
- Tray contents get mixed up when returned to CSSD.
At the tray tracking level, you are less concerned with what instrument is packed, but more of what type of instrument is packed. For example, it doesn’t matter which sponge holder is packed as a long as a sponge holder is packed.
However, with instrument level tracking it now needs to be the exact sponge holder. You can't just pack any sponge holder.
Consider this; tray level tracking means that you just need to count off the required number of instruments to fill up a tray.
Tracking at individual level however, means you need to find, match and count the exact instrument ID’s on the instruments as listed on the tray List.
Because the instruments are barcoded, you can scan each instrument to aid in the set-up process. But remember that this will still take time. For example, if a tray has 80 items, that’s 80 instrument barcodes that need to be scanned.
If you are dealing with mixed up trays, then you’re going to need to sort them out first.
Simply just implementing individual instrument tracking at setup will require more than your current amount of effort to process items. So, unless you strategise around this reality, this will slow you down.
Some of the strategies that you can put in place to minimize the impact on effort are:
- Etch a human readable Tray code on the instruments when you etch the 2D Data matrix barcode
- Keep your sets together
- Accept that tracking to the highest level will take more time
When you etch a 2D data matrix barcode on an instrument, it will look something like this:
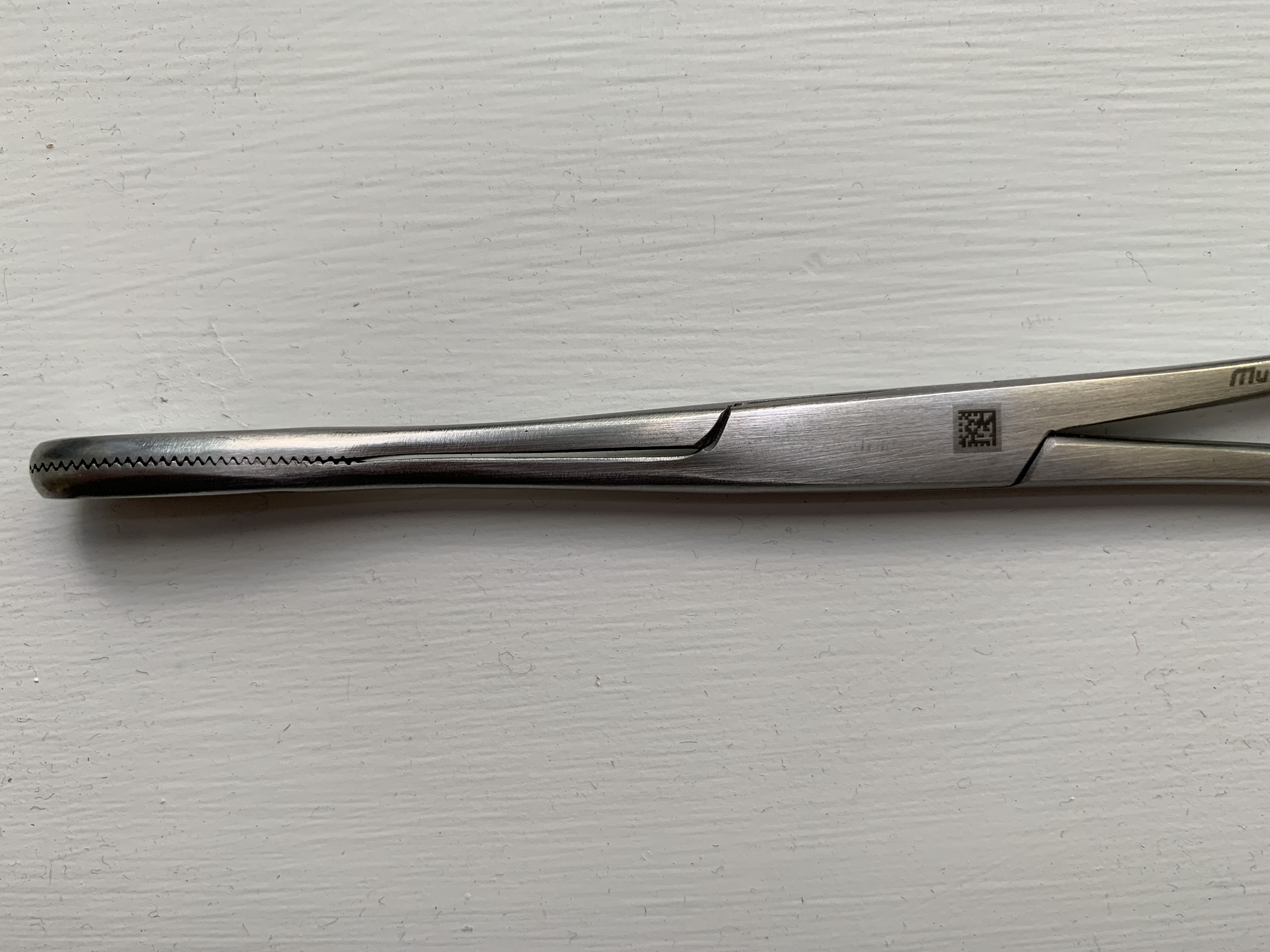
As you can see it’s a code that requires a 2D reader to scan it before you will know what the code is. Remember, you’re going to need to scan a bunch of these at setup and if the trays are mixed up you’re going to have to scan them to sort them first.
Etching human readable codes will speed things up significantly.
First, it’s a good idea to etch the actual ID of the instrument below the 2D barcode. This means you can identify the instrument without the need for a 2D reader if needed. ‘GT 1’ – is an example of a tray group code. This will allow the technician to quickly find the identified instruments for a particular tray (in this case it's general tray 1) amongst a bunch of mixed up instruments.

Conclusion
Regardless, of whether you want to go to tray level or instrument level tracking, it’s a good idea to carefully consider what each entail so you’re not surprised later. Remember, both will give you tracking system compliance to AS/NZS 4187:2014.
One of the biggest myths about instrument level tracking using 2D Data matrix barcodes etched on instruments is that it will simplify and speed up your processes. This is simply not true.
You will however, be tracking to the highest possible level.
Just lastly, when considering which level to track at and what processes you want to track, consider the benefits versus the effort.
Remember the more you want to do, the more you will have to do.