AS4187:2014 – Do paper based tracking systems still cut it?
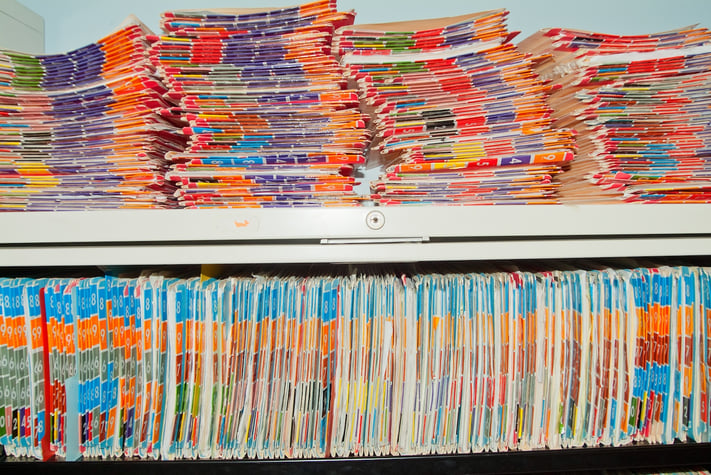
Last month our Company attended the WHFSS conference in Brisbane as an exhibitor. While I was there, I had a number of interesting conversations with delegates who were using paper based tracking systems and were feeling that the new requirements of AS4187:2014 were going to substantially increase the amount of paper work that they would need to complete.
Some delegates were quite anxious that their paper based system just wouldn’t cut it anymore. Hence their discussions with us.
Speaking with other exhibitors, I found that I wasn’t alone in my perception about the levels of anxiety that I had detected as they had also experienced a similar feeling amongst many of the delegates they spoke with.
Lucky for all in Australia, we have time to further plan, as the deadline for compliance has been extended by the Australian Commission on Safety and Quality in Health Care to 2021.
But the question that was raised is very interesting: Given the extensive additional requirements of the new standard, do paper based tracking systems cut it anymore?
Product Families
One of the most significant changes is the introduction of product families.
When assigning an RMD to a product family, you must consider and document the:
- materials
- design
- physical characteristics
- packaging.
You can see my blog here for more details.
But the interesting thing here is that unlike ISO/TS 17665-3 product families just don’t relate to steam sterilization. The new sterilizing standard relates product families to all cleaning, disinfecting, packaging and sterilization processes.
This means you need to document a methodology for assigning RMD’s specific to washing and disinfecting processes.
Decontamination
But it means much more than that. You will need to be able to ensure that an RMD assigned to a specific product family is not processed through an incompatible cleaning or disinfecting process. And that means tracking and recording every process event.
So if you're using a manual paper based system it now needs to extend to the decontamination (dirty) area. As paper is made of cellulose fibres and is particularly absorbent and decontamination areas are generally wet and…...well dirty, filling out paper records there is less than ideal.
Storage, retrieval and Recall
Manual paper based systems all have one thing in common. They all require physical storage space. Once the form is complete, it needs to be filed away for a specific period of time to comply with statutory minimum record keeping standards and, of course, in case of recall and audit.
Forms filled out in decontamination areas are no different. The will need to be stored somewhere and its most likely that they will need to be transferred to a clean area for storage and future retrieval. This is clearly not ideal given that they may need to retrieved and handled in the clean area of CSSD. But worse than that, in the event of a major incident, they may need to be handled in other areas such as medical records and administration.
Check out our new guide:
Manual Cleaning and disinfection
For each use of the instrument grade high level disinfectant you must monitor and record:
- The temperature of the HLD
- Contact time
- Rinse water volume
- MRC
If your using a paper based system, things just got even worse.
Here you are gloved up and in full PPE in a dirty area, washing and disinfecting items by hand, and having to complete results of the process as you go with a pen and paper.
No matter how you look at this, it’s clearly not ideal.
For endoscopy reprocessing, the requirements are similar.
Conclusion
The general feeling I got from delegates at the conference who were using manual paper based records systems was that they felt their current systems were somewhat inadequate and that they ‘really needed’ to do something about it.
The minimum required records that you must keep is now quite extensive.
Records at a minimum shall include the following:
- Monitoring of reprocessing equipment.
- Cleaning process records.
- Sterilizing process records.
- High level disinfection, including chemical and thermal process records.
- Microbiological surveillance testing (where applicable).
- Cleaning of reprocessing equipment.
- Cleaning of the reprocessing facility.
- Maintenance records for RMDs (where applicable) and reprocessing equipment.
- IQ, OQ and PQ for reprocessing equipment (where applicable).
- Process deviation reports and where applicable, records of corrective action or preventative action.
And that’s a lot of paper work! Oh and storage.